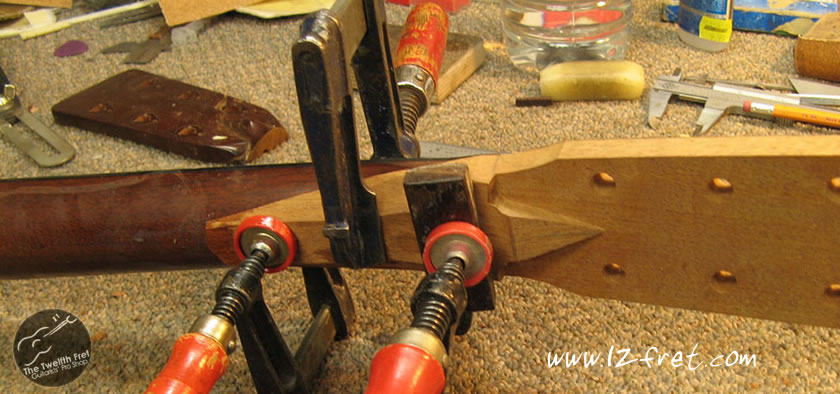
Restoration
The question of instrument restoration regularly comes up at the repair bench. Here, we’ll talk about the broadest outlines of restoration and repairing and look closer in upcoming episodes.
Many people who have older, often badly worn or damaged instruments, and especially inherited from family members, want to know about restoring them to playable or new condition. Answering these questions requires looking at all the aspects of what’s happened to the instrument over time, what outcome is hoped for and what is physically possible. That is then balanced against what any historic or sentimental value the instrument might have, the resulting monetary value, and finally – the cost. On antique instruments, costs can be spectacular since parts must be custom made and rare materials used.
Most of the time, the decision rests on the balance between the cost of the work and the resulting monetary value. The major repairs normally part of a restoration can quickly become overwhelmingly expensive. As well, some types of repairs or restoration, especially finish repair, reduce the value of a vintage or antique instrument.
The rule of thumb for monetary value is that regardless of appearance, if the instrument is playable its value is higher with all, and only, the parts and finish it had when it left its maker. Exceptions involve who played the instrument and when.
The final question after cost is whether to restore to working condition or original condition.
We should look first at what restoration is, and how it differs from repairs. Restoration is the whole action of taking something back to the way it was at some point in time, often to its condition when new, or at some historically significant point. Repairs are fixes to specific problems and don’t address the whole as restoration does. It’s important to note that repairs can also move away from the idea of restoration to original when original contained flaws or weaknesses, or used out of date or even currently illegal materials like ivory.
A common example of a repair moving away from restoration to original is replacing or repairing a bridge plate on a steel string acoustic guitar. The bridge plate is on the inside of the top, under the bridge, with the holes for the bridge drilled through it. The plate has two purposes: to provide a hard surface for the metal ball end of the string to catch on with the bridge pin pushing the ball forward and provide stiffness to the top at the center of tension. Without the plate, the ball end will rapidly wear through the soft wood top and rest against the bottom of the bridge itself. Soon, the bridge is lifting and can pull right off, causing extensive damage.
Some guitar builders used thin hard wood or laminates, also known as plywood, for the bridge plates and interior laminate layers are softer wood like poplar. Unfortunately, woods often splinter when drilled so the holes are thinner than they seem. Over years and many string changes, the holes are so worn that the plate isn’t serving the purpose of holding the ball end of the string. And, if it lacks stiffness the top may have ‘bellied’.
The repair concept is to pry off the bridge plate and install a new one but this can be surprisingly difficult and damage the top itself because of the phenomenon of grain run-out. Run-out means that the wood cells run at an angle to the surface, so the prying tool digs into the top rather than breaking the glue layer.
Frequently the real repair is to add a sub-plate made of maple or rosewood, essentially a hardwood band-aid covering the area required for the string holes.
This repair solution is to the point, relatively quick and inexpensive. In restoring the instrument to working condition, it does not restore to original condition, which would restore the original flawed materials choice. Still, this approach doesn’t prevent later restoration to original.
For a rare example, consider the original 1952 Gibson Les Paul model. The first production used a trapeze-mount bridge and tailpiece that is peculiar to a very few years. This part dictated a very shallow neck angle, and for the way most people now play, the strings are unworkably high. It’s possible to rework the neck joint to make the guitar play according to modern needs, though this is an irrevocable change. The instrument can never be restored to its original condition.
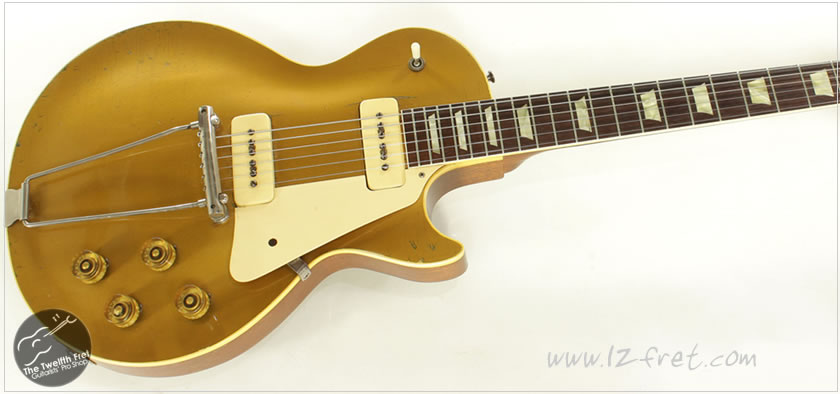
Restoration
Finally, let’s look at finish restoration, a very common request. Until the late 1960’s, most production guitars and mandolins used sprayed-on nitrocellulose lacquer finishes, unlike violins which used varnishes. Nitro lacquers have many drawbacks, including extended curing times that slow production and increase cost. With use, they wear off and with normal temperature and humidity changes, they crack and “check”. Modern poly finishes are much more robust. Damage to either of these types of finishes can not be easily repaired or restored, so replacing the finish seems necessary to get the original look. Refinishing requires stripping and sanding, which can easily change contours and thicknesses. Reproducing an original look is high art and very expensive.
Next time we’ll look at issues around replacing metal parts, wiring and electronics.
~Patrick Keenan – The Twelfth Fret